We recently improved our ToF decoding pipeline (firmware) and also ToF factory calibration, which has been applied to our latest OAK-D Short Range PoE with ToF cameras.
Pointcloud!
Here's a raw pointcloud (we haven't applied any postprocessing filters) directly from the camera.
ToF Accuracy
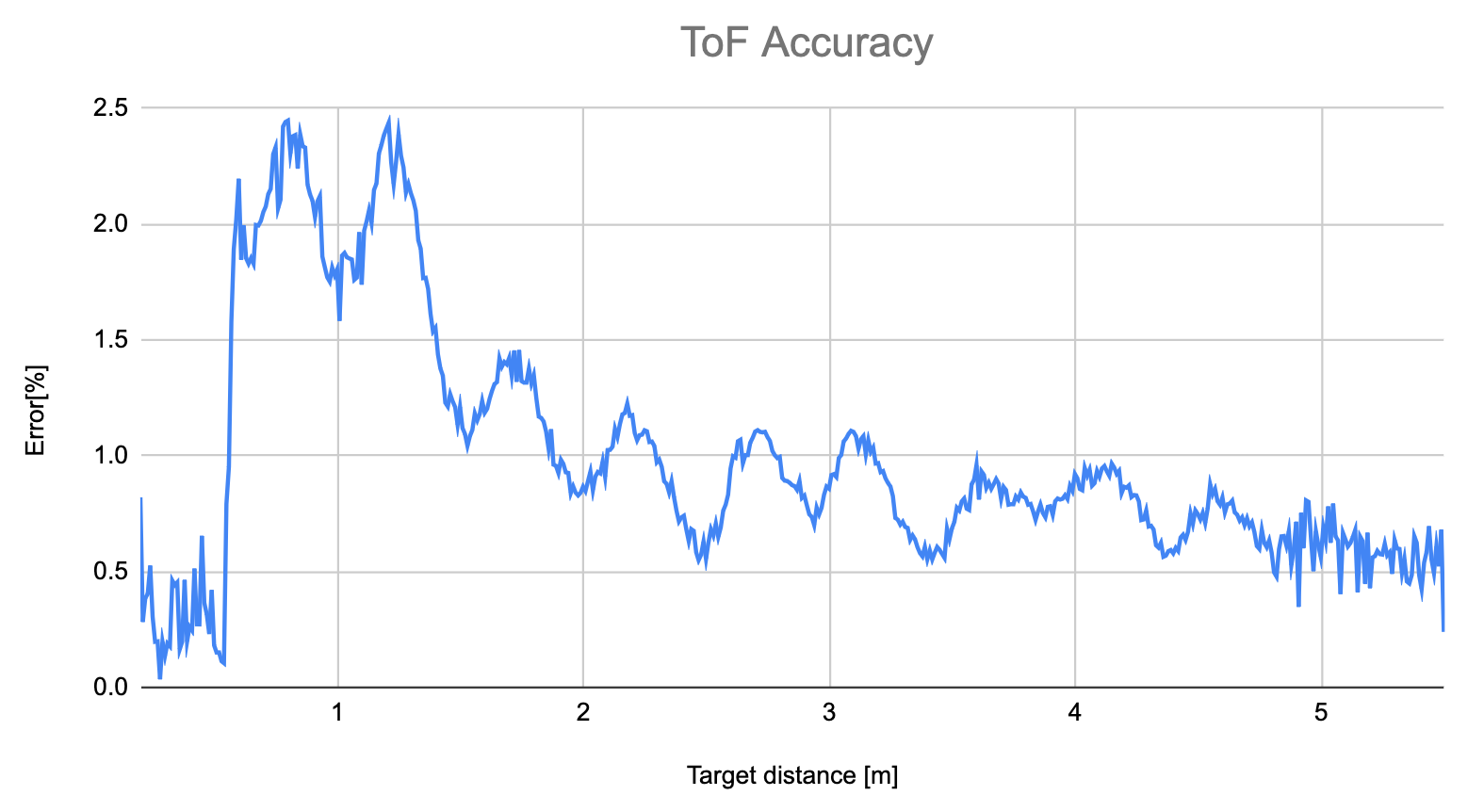
The ToF depth error graph, measured on a factory-calibrated OAK-D-SR-POE camera.
About iToF systems
Indirect Time-of-Flight (iTOF) is a measurement technique used to determine the distance between a sensor by emitting an IR light wave that travels to the object and then back to the sensor.
While traditional TOF directly measures the time it takes for a signal to travel to an object and back, iTOF indirectly estimates distance through the analysis of intensity or amplitude modulation of the reflected signal.
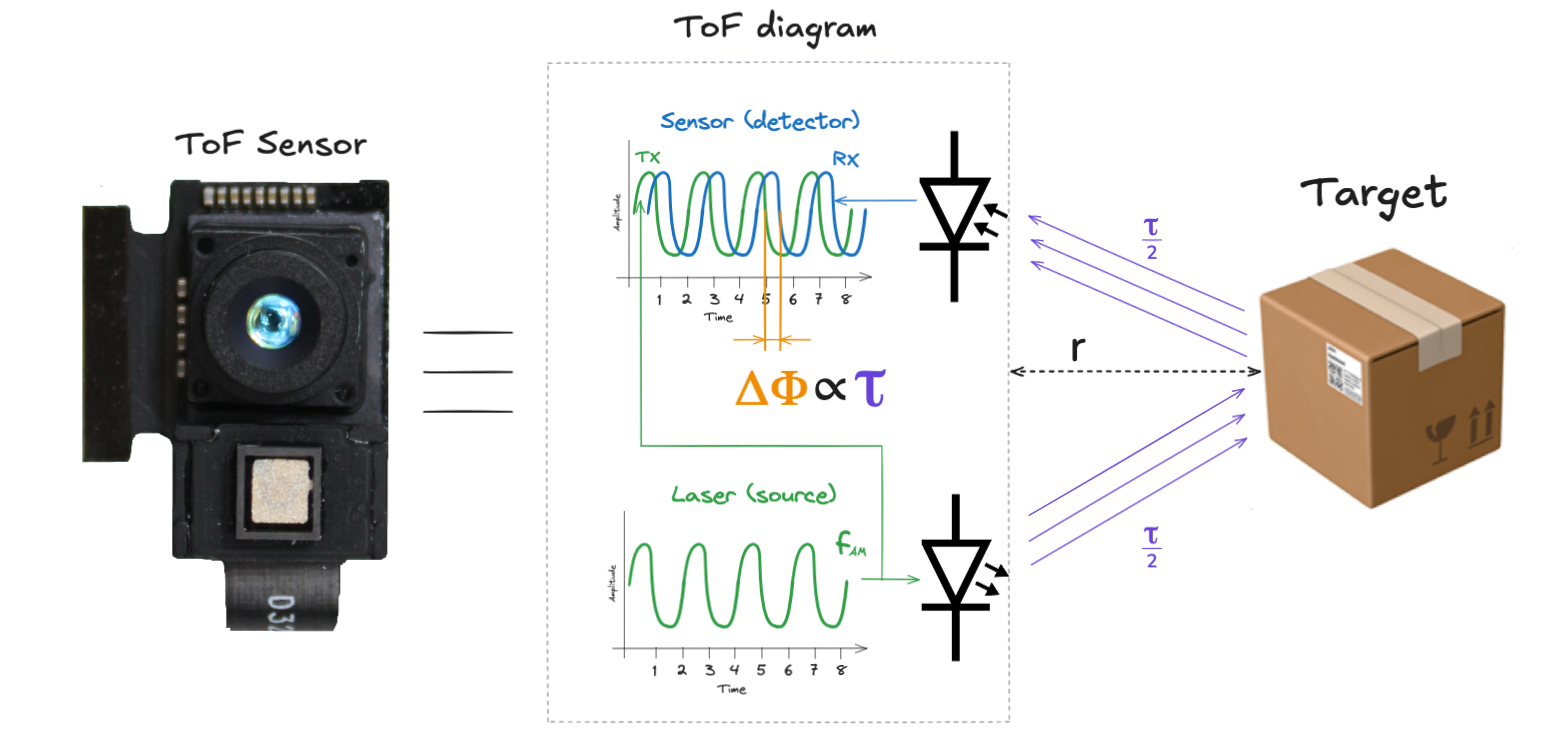
As the signal travels to the object and back, it undergoes changes in intensity or amplitude. These changes are caused by various factors, including the object's surface properties, distance, and environmental conditions. The sensor analyzes the modulation pattern of the reflected signal to extract information about the distance to the object. By correlating the modulation characteristics with known parameters and calibration data, the iTOF system calculates the distance between the sensor and the object.
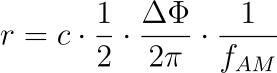
The distance to the target is directly proportional to the phase shift (ΔΦ) for the given modulation frequency, in our case either 80MHz or 100MHz.
Phase Unwrapping
In iTOF systems, measuring longer distances accurately can be a challenge due to modulation frequency used.
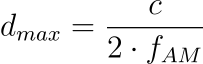
The ToF system we are using supports modulation frequencies of 80 MHz and 100 MHz, which means the maximum distances that can be measured are 1.875 meters and 1.5 meters, respectively.
For example, if a target is 2.8 meters away, the system using only a 100 MHz modulation frequency would be unable to distinguish whether the target is at 1.3 meters, 2.8 meters, 4.2 meters, or beyond, as it can only detect the phase shift and not the exact distance
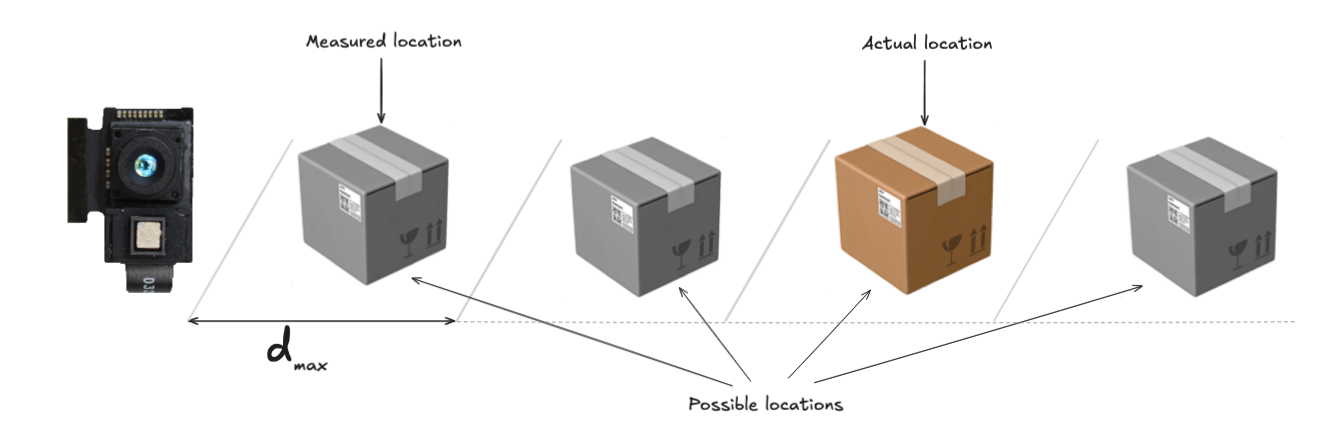
Using both modulation frequencies (80 MHz and 100 MHz) in an iToF system can help extend the maximum measurable distance beyond the limits of each frequency individually. This technique leverages the principle of multi-frequency phase unwrapping to resolve distance ambiguities.
Noise and Errors
To minimize the noise and error, each ToF sensor is calibrated during our factory calibration. We have recently improved this calibration, so it can compensate for different errors that are present in ToF systems.
Fixed Phase Pattern Noise (FPPN)
This type of noise occurs due to imperfections or inconsistencies in the TOF sensor components or environmental factors. These imperfections can be seen as systematic errors in the phase measurement. During calibration, the system measures the phase shift when no object is present (background phase) and calculates a correction to be used. Each camera has a different FPPN correction, which means that each camera needs to be individually calibrated to compensate for it. Without this compensation, the depth output does not have the necessary quality to be of any use.
Harmonic Aliasing (Wiggle Error)
The wiggle error is a result of using phase unwrapping. Ideally, the emitted signal would be a perfect sinusoidal wave, but in practice, we use square waves. When square waves are used, the resulting cross-correlation takes on a triangular shape and this triangular waveform introduces higher frequencies, which can alias or distort the primary harmonic signal. The consequence of this aliasing is a "wiggle" or non-linearity in the measured distance.
In practice, this error makes straight surfaces look “wiggly”. For illustration, please see the following picture taken from a raw depth map showing a side view of a desk. Sometimes this error can be hard to see for the human eye, but its correction is a key feature for improving the quality of measurements of ToF cameras.
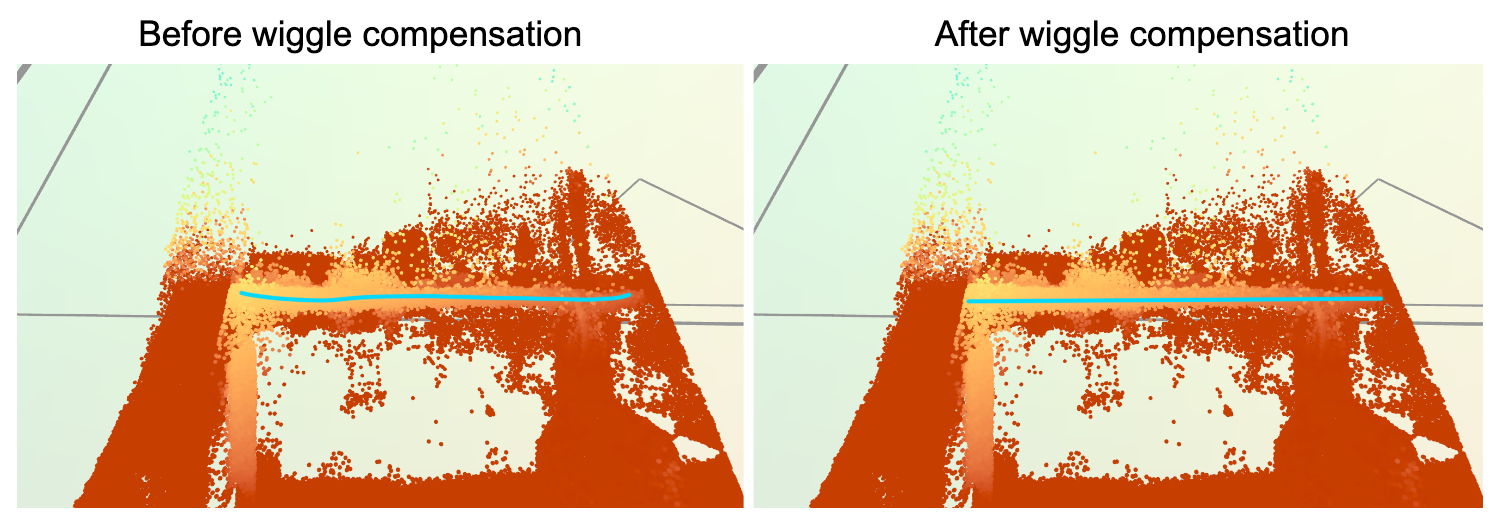
I hope this blog post has been interesting, let us know your thoughts below🙂